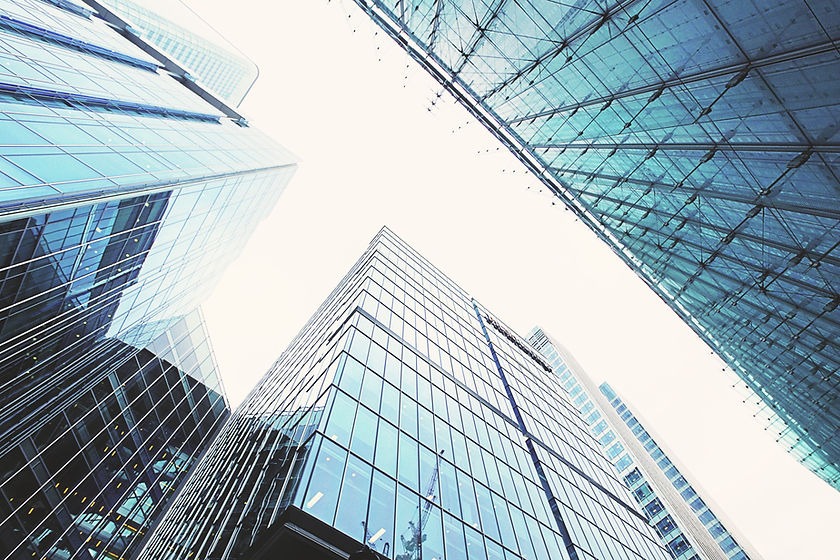
Achieving success
Past and present clients
Project managed a high-profile / top priority project for the Tropicana Brands Group / PepsiCo with very challenging timescales and a diverse stakeholder group across multiple countries.
​
-
The goal of the project was to robustly implement a supply chain solution for a new ambient product range for Tropicana to compliment the existing chilled range.
​​
-
The scope included setting-up a new plant in SAP (development, configuration & testing), extension of master data and the development and implementation of new processes for inbound, outbound, admin / inventory & customer work-streams.
​
-
Following the rapid establishment of robust cadence, project organisation & controls (including a detailed project plan, RAID Log, weekly Highlight Report, go-live criteria, stakeholder engagement matrix and training & comm’s plan), the project was a great success.
​​
-
The new plant in SAP was implemented in the FASTEST EVER time-scales in history of the PepsiCo Global Template (PGT).
-
Hyper care is now complete, lessons learned have been collated and a robust project closure and handover to business-as-usual has been completed.
​​
-
I am now available to start a new assignment, preferably a short-term contract.
​
​
​The key focus of the assignment was the robust planning and delivery of several new high-priority, customer acquisition projects with the following clients: Hartmann (a leading healthcare product supplier) and Emtelle (a global manufacturer of pre-connectorised, blown-fibre cable and network ducted solutions) and Ingram Micro (the world's largest global business-to-business wholesale provider of technology products and supply chain management services).
​
-
Project managed the implementation of a new business implementation, where Yusen Logistics took over the distribution of Hartmann products in Heywood, Manchester with local fleet and a network transhipment solution for the rest of the UK, working in partnership with Menzies Distribution.
​​
-
Facilitated the completion of UAT, business readiness, implementation and post-go-live support of an integration between Emtelle's AX ERP system and Yusen's transport management system.​
​​
-
Led the project definition, planning. implementation and post-go-live support for a third-party transhipment operation via Yusen Logistics Leeds and Derby to transform Emtelle's logistics operation, delivering improved controls, better service and enabling opportunities for future growth.
​​
-
Facilitated the definition, planning and initial implementation of a project to centralise the storage and distribution of Emtelle products manufactured in Scotland at Yusen Logistics Derby.
​​​
-
Facilitated a high-priority transition support project to facilitate operational stabilisation for Ingram Micro. Provided a robust structure, cadence, tracking and issue resolution to close down cross-functional challenges and enable continuous improvement.
​
​
Defined, mobilised and managed a transformation programme at one of Clipper Logistics flagship Ancillary Distribution Centres, which houses John Lewis Pre-Retail, Forward Orders and Returns and several other third-party contracts including Inditex, Levi's and Zara Home.
The key focus of the assignment was to improve the efficiency of the John Lewis operation and develop the team’s capability to deliver robust business change.
​
The programme comprised three projects focused on organisational restructures, five involving process re-engineering, three involving systems & hardware changes and one focused on layout optimisation:
​
-
A review of the organisational structure of the administration, reporting and inventory functions. This resulted in some restructuring, enabling better capacity within the stock inventory team and the implementation of improved inventory controls.
​
-
A review of e-Commerce returns tracking, which resulted in the roll-out of new hardware, reporting and systems changes. This enabled better visibility and control of the dwell-time for inbound returns stock.
​
-
A review of the Returns operation, working with the operational team to develop a detailed proposal for an optimised layout, using automation to improve flow and efficiency.
​
-
The development and implementation of a bespoke query management system for the online returns operation.
​
-
A review of the site intake & despatch functions aimed at centralising these to deliver better controls and improved efficiency.
​
-
Development of a bespoke change management methodology based on PRINCE2 and coaching the team on how to robustly approach and deliver change.